As Covariant co-founder, President, and Chief Scientist, Pieter Abbeel, mentioned in a recent interview, automation in today’s warehouses tends to be focused on the “legwork” — largely conveying items from one part of the warehouse to another. Automated unit sorters (e.g. split tray sorters, bomb bay sorters, tilt tray sorters), pocket or pouch sorters, and even AGV or AMR-based sorters are often used as part of this conveyance.
But the process of placing, or inducting, items onto the sorters and conveyors, is largely manual — that is to say, the “handwork” remains unautomated.
This manual induction is a highly repetitive task prone to injury and high turnover rates, which make it difficult to staff. Additionally, inaccurate placement of items on the sorters can lead to frequent jamming resulting in stoppages affecting throughput.
Now, with advancements in modern deep learning-based AI, that is changing. AI-powered robots can now autonomously pick and place virtually any type of item or SKU, regardless of shape, size, packaging, and variety.
What is robotic induction?
A robotic induction system uses AI-powered robots to autonomously induct items onto sorters, rather than having a person perform this repetitive injury-prone task. AI Robotics platforms, such as the Covariant Brain, enable robots to perform this task with high precision at high speed and accuracy over sustained periods of time.
Why is artificial intelligence needed for this task?
Because it’s hard! We take it for granted as humans. But for a robot, picking up an item requires understanding its size, shape, and deformability, rapidly doing complex math problems to calculate the angle of approach and the optimal path to a destination, and placing the item with a degree of accuracy and care that will ensure that the item doesn’t fall off the conveyor or sorter (that’s moving!) or break in the process. And that’s just for one SKU – humans in these positions process hundreds of thousands of SKUs, all of which have different shapes, dimensions, and materials, and can switch to picking and placing totally new SKUs in an instant.
Our AI Robotics platform, the Covariant Brain, enables a robot to do all of this with high speed and accuracy, to learn from its mistakes, and to pass its knowledge on to all other Covariant robots in the network. Robotic sorter induction takes advantage of this ability to complete pick and place tasks with precision.
Four Key Components of a Robotic Induction System
AI-powered picking for any SKU type
When it comes to robotic piece-picking at warehouses, the sheer variety of SKUs and items can present virtually infinite combinations of variations: shape, size, deformability, transparent packaging, mixed-material packaging, and so on. Add to that SKUs rotating seasonally, especially in apparel and fast fashion.
This is precisely where modern deep learning-based artificial intelligence (AI) excels: in using all these variations – literally billions of data points to train on. The Covariant Brain leverages this training to enable robots in warehouses around the world not only to perform pick-and-place operations like sorter induction but also to learn and improve from each other continuously over time.
Induction onto a variety of sorters
Any robot you integrate into your induction process will need to adapt its placement tactic to match the way your existing system operates. As such, it’s important to look for a robotic system that will work with your existing sorters, whether you have a Eurosort split tray sorter, a KNAPP pocket sorter, or a Tompkins AGV-based tSort.
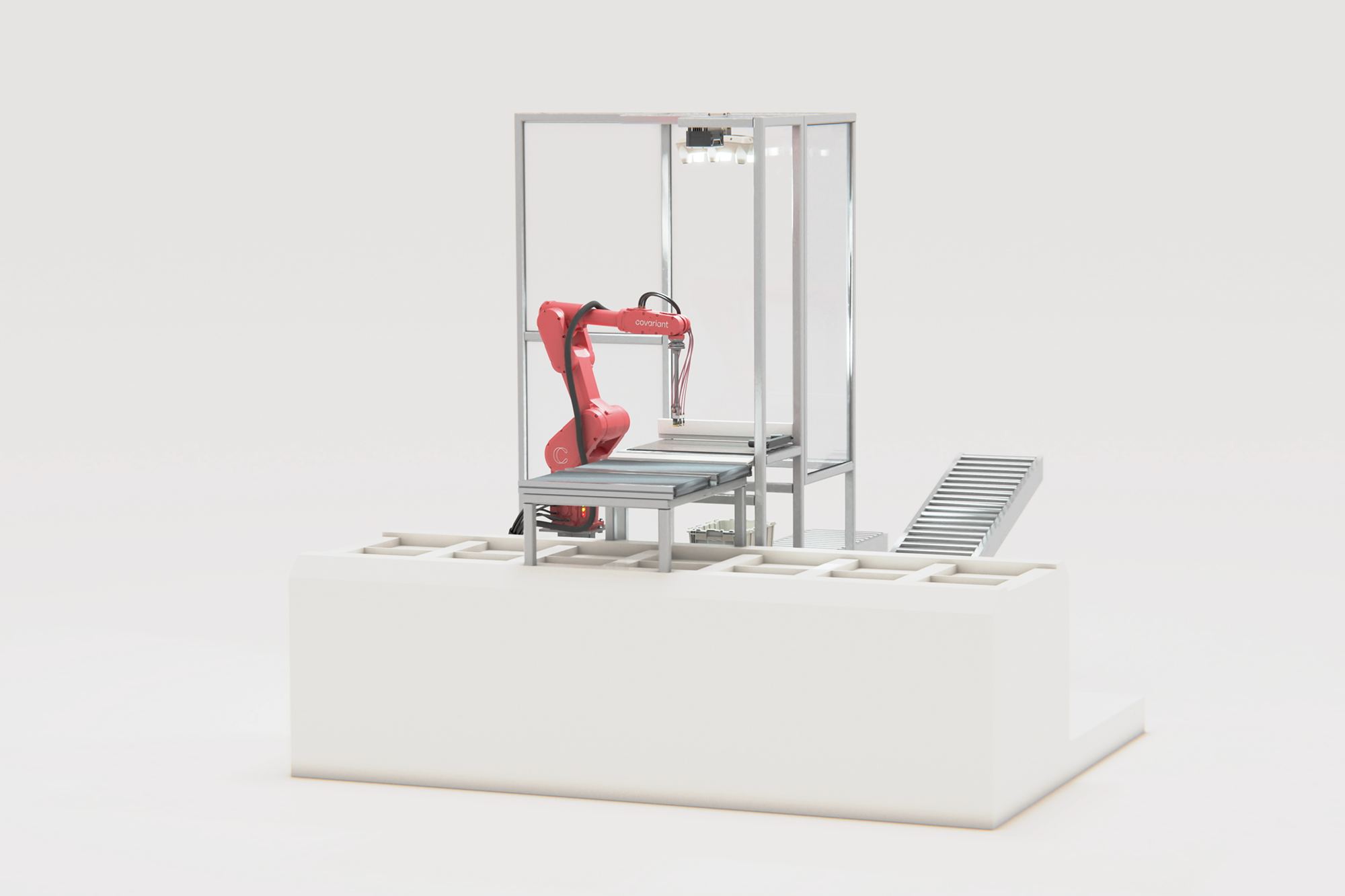
Speed and precision
In both manual and robotic operations, it’s not uncommon for sorters to jam due to inaccurate placement of items, leading to downtime. Oftentimes, this occurs when there is a fast-moving unit sorter where the person or robot doing the placing struggles to drop the item they’re placing in the exact right position as the belt or tray moves by quickly. Accounting for this with a robotic system takes purposeful and innovative solutions designed to not only match the speed of a person performing inducting but also increase accuracy.
For example, at Covariant, we’ve designed one sorter induction solution specifically to induct onto fast-moving sorters. We use a top-mounted accelerator that drops the item onto an empty sorter slot with accuracy. Because it is designed with apparel in mind, the item is dropped flat, without bunching up and risking jamming the sorter. See the video below for an example.
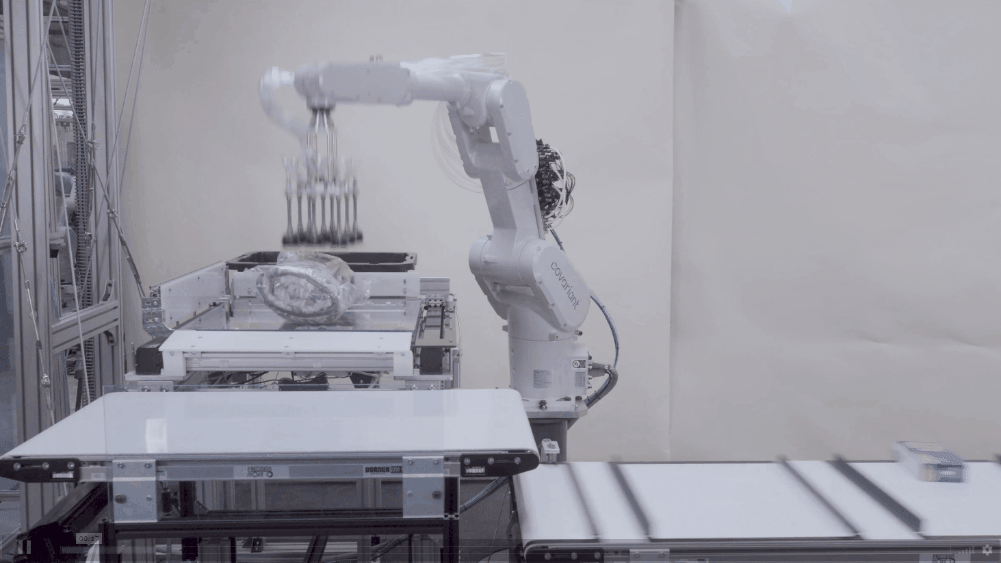
Seamless integration
A robotic induction system should be tailored to specifically fit into your existing operations and workflow without requiring disruptive floorplan reconfiguration and workflow changes. It should work not only with the type of sorter you have but also with your existing systems, like your warehouse management system (WMS) and order management system (OMS).
Robotic Induction: The smart investment for your warehouse operations
In times when e-commerce demand continues to fluctuate, and finding labor can be challenging, investing in AI Robotics can help you continue to increase operational efficiency. Covariant’s robotic sorter induction is the perfect solution to help take your automation strategy to the next level.