Depending on the order volume and existing material handling processes, manual putwalls can often be used by apparel retailers and their logistics providers for sorting batch-picked orders. A put-to-light or similar system might be used to increase sorting accuracy as well. However, as it continues to be a challenge to hire and retain labor in the face of high order volumes, this manual process can hinder shipping throughput.
In order to meet customer expectations around shipping and delivery times, a robotic transporter putwall can help reduce labor-related bottlenecks.

What is a robotic transporter putwall?
Instead of having someone manually sort batch-picked items into a putwall, a robotic putwall can automate this process. Using AI-powered robotics, individual items can be picked from a mixed-SKU tote, have their barcodes scanned, and then delivered to the corresponding order bin in the putwall.
Notably, the robotic transporter putwall supports polybagged apparel, parcels, and other items using a transparent scan table and mechanical shuttle system to sort goods at very high speed leading to productivity and capacity gains.
In solutions like the Covariant Transporter Putwall, the shuttle system increases throughput as item transfers to bins are parallelized while the robotic arm is tasked with just picking and placing items quickly for them to be scanned and destination bins assigned.
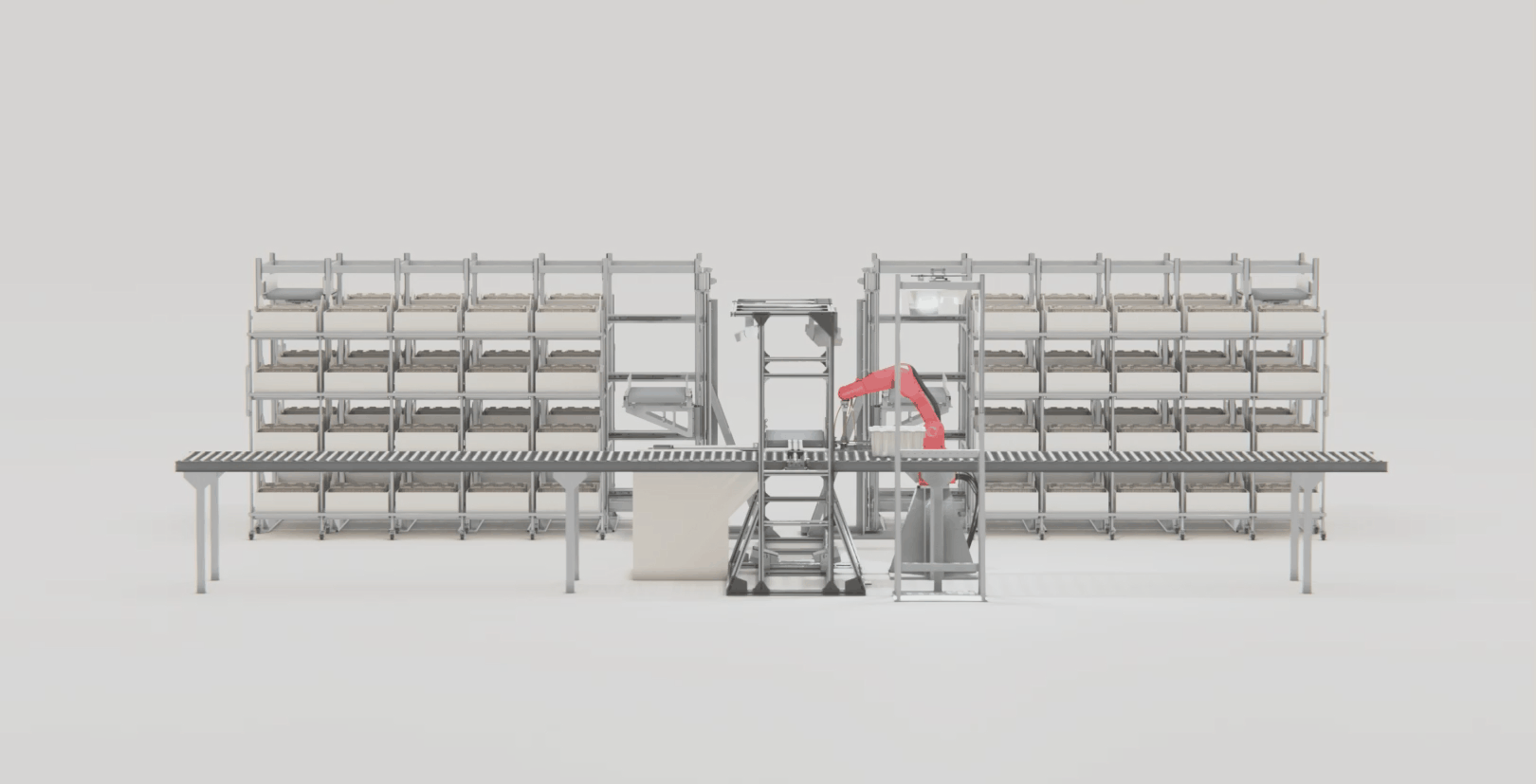
Three key aspects of a robotic transporter putwall
AI-powered piece-picking
When it comes to picking up apparel items, robots have to address a very complex scenario due to the unique dynamics introduced by the shape, packaging, and deformability of apparel items. Apparel in transparent polybags can be floppy and unwieldy, making them difficult for robots to successfully grasp and transport. On top of that, in batch-picking operations, robots will likely experience mixed-SKU totes with polybagged apparel items chaotically strewn about, overlapping each other.
In order for robots to successfully handle such apparel items, modern deep-learning-based AI is required. A universal AI Robotics platform, like the Covariant Brain, uses vast amounts of data from connected robots around the world to enable robots to handle apparel with high speed and accuracy from Day One. Additionally, the Covariant Brain uses our propriety vision system to generate 3D visualizations with the high precision and fidelity required to prevent accidental double-picks and improve picking accuracy for chaotically organized mixed-SKU totes full of polybagged apparel.
Scanning and gripping
While universal AI, such as the Covariant Brain, helps robots understand the picking scenario and identify the best way to pick up and move an item, key components of the robotic station ensure the item is successfully scanned and delivered to the destination order bin with high speed and accuracy.
A specialized end effector is needed to be able to handle the often floppy and unwieldy apparel items. Using individually actuated suction cups ensures that only the targeted item is picked, avoiding adjacent items, and further reducing double-picks and unsuccessful picks.
Another key part of the process is barcode scanning, which can be challenging with apparel items as the barcode can be placed anywhere on the item, on the outside or inside of the polybag. To address this, solutions like the Covariant Transporter Putwall use a scan table with multiple barcode scanners above and below the item, resulting in fast error-free readings.
In combination with specialized end effector and scanning, novel automation mechanisms transport scanned items to the order bin with high speed and accuracy.
Designed to fit into your operations
Robotic solutions should integrate seamlessly with your existing warehouse operations to ensure minimal disruption to your current upstream and downstream processes. Upstream, the robotic stations should interface with the WMS and OMS to access the order information and tote details. Once an item is scanned, the OMS should be queried to identify the correct order bin. And finally, once an order has been completely picked, any packer notification (put-to-light, etc.) is triggered to let the packer know the order is ready for packing. Covariant’s Transporter Putwall also allows for removable shelves on wheels if your operation requires it.
Collaborating with your team, your robotics solution provider should deliver a holistic solution that works seamlessly with your current operations.
Robotic Transporter Putwall: Driving operational efficiency
Manually sorting apparel SKUs in your batch-picking operations can be labor-intensive and difficult to staff. AI-powered solutions like the Covariant Transporter Putwall help reduce your labor dependency and costs while increasing efficiency in your warehouse operations.