To maximize space and increase efficiency, warehouses have implemented goods-to-person (GTP) systems such as the Autostore cube storage, the KNAPP EVO shuttles and autonomous mobile robots (AMRs) to pick and bring goods to people for picking out of a tote.
But there’s another way to increase efficiency that has become possible with AI Robotics: by turning goods-to-person systems into goods-to-robot systems.
What is robotic goods-to-person picking?
A goods-to-person system delivers items directly to a prepping and packing station rather than having a person retrieve them individually. This reduces footsteps, keeping workers focused on a single task, while the automated delivery system optimizes speed and efficiency.
Robotic goods-to-person picking places an AI-powered robot in the role of prepper and packer. Major warehouses around the world are already deploying robotic goods-to-person systems to increase throughput and lower costs.
Spotlight: McKesson
McKesson, the largest pharmaceutical wholesaler in the United States, wanted to bring more automation to their operations. They chose the Covariant-powered KNAPP Pick-It-Easy Robot as their solution. The Covariant Brain quickly learned the broad and ever-changing SKU mix, which the robot picked with precision via individually actuated suction cups – essential when picking small and oddly shaped pharmaceutical items.
Three key components of a robotic GTP system
1. AI-powered picking
Modern deep learning-based artificial intelligence (AI) is what powers robots in warehouses to perform pick-and-place operations autonomously and should be a core component of any robotic GTP picking system you may be considering.
The Covariant Brain, for instance, is the leading AI Robotics platform that powers robotic GTP picking systems around the world. Trained on millions of picks from connected robots, the Covariant Brain enables robots to perform with high speed and accuracy out-of-the-box across a broad item mix, regardless of size, shape, and packaging. And they continue to learn and improve over time.
2. Workflow integration
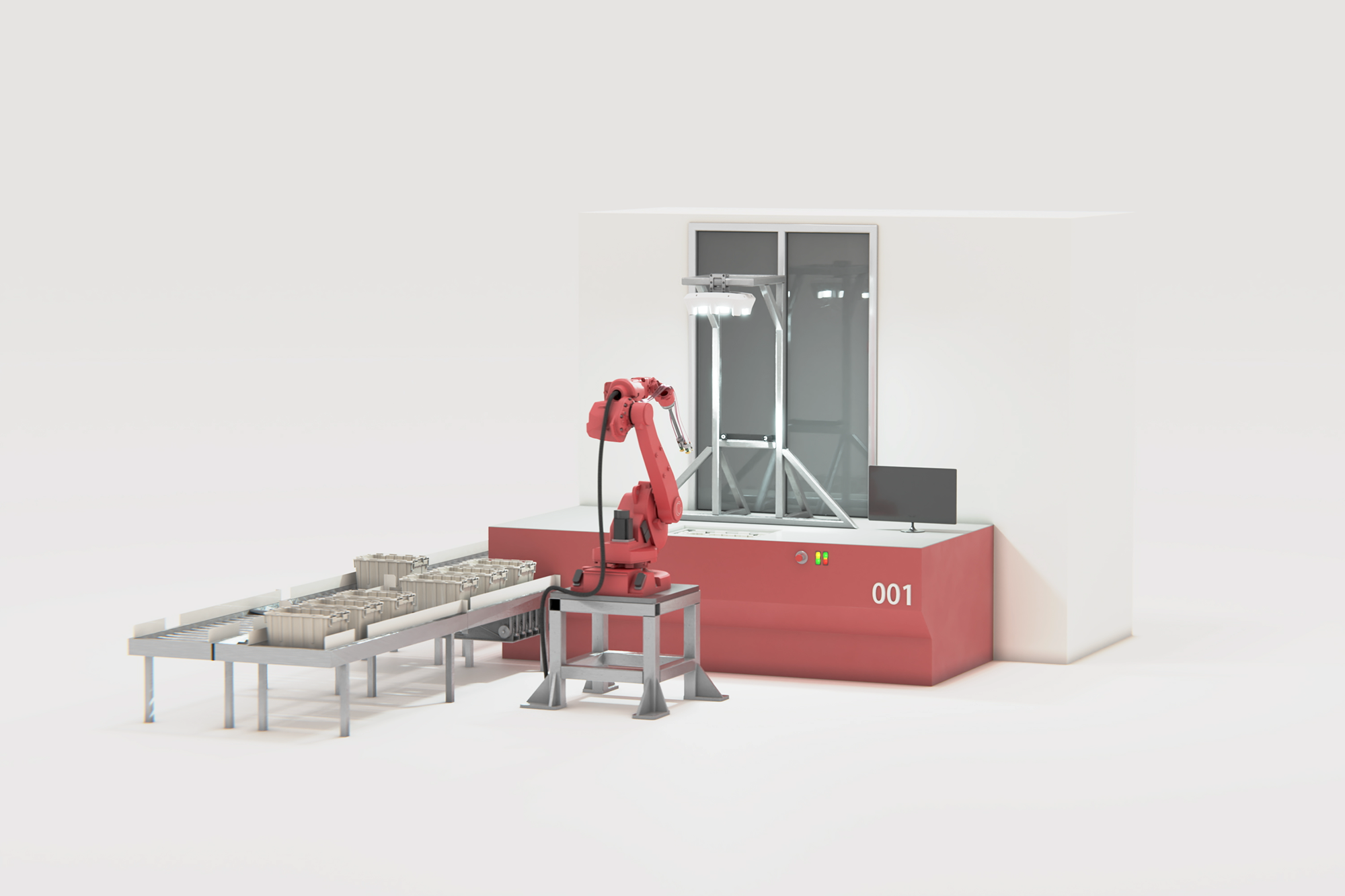
A robotic picking system should integrate easily with the existing goods-to-person system’s station layout using an industrial robot or a cobot. It should also seamlessly interface with existing materials handling workflows for upstream and downstream processes (e.g. conveyors, AMRs) and existing systems (e.g. warehouse management system, put-to-light).
And in all of these systems, there should be full access to a manual station as a backup so a human can work alongside a cobot if needed.
3. Matching system speed
It’s critical that the robot you deploy be able to match the speed at which your GTP system presents totes. This ensures that there aren’t any slowdowns to your upstream and downstream processes and that the solution is operationally viable.
Now is the time to invest in robotic GTP picking
Covariant-powered robotic goods-to-person systems offer out-of-the-box autonomous performance with high throughput and accuracy. In today’s economy, where demand is volatile, labor needs are difficult to predict and labor itself is hard to come by, automating your goods-to-person system can provide the stability, predictability, and efficiency needed for navigating today’s markets.